Hot chamber die casting is an efficient and widely used pressure casting process for manufacturing metal components. This process is mainly applied in the production of low-melting-point alloys such as zinc, lead, and tin. Its core principle involves directly injecting molten metal, eliminating the need for external metal supply.
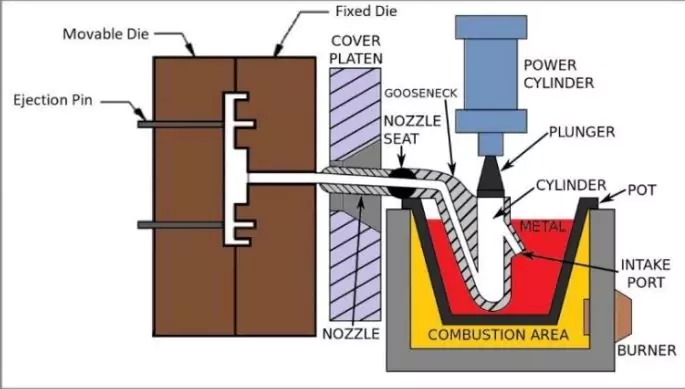
Firstly, the key to hot chamber die casting lies in the storage and supply system for molten metal. The hot chamber die casting machine consists of a furnace containing molten metal, a sealed injection chamber, and a pressure chamber. At the start of the process, the metal in the furnace remains in a liquid state and is injected into the mold through a nozzle in the sealed injection chamber. In the injection chamber, metal is pressurized and injected into the mold to form the specific shape of the desired part.
Compared to cold chamber die casting, one of the main advantages of hot chamber die casting is its production efficiency and lower energy consumption. Due to the liquid state of the metal throughout the process, cooling time is reduced, resulting in shorter production cycles. Additionally, as there is no need to reheat the metal in every cycle, hot chamber die casting has lower energy consumption, helping to reduce manufacturing costs.
However, hot chamber die casting also faces some challenges. Firstly, the process is primarily suitable for low-melting-point alloys, limiting its application in the production of high-melting-point metals. Secondly, the direct connection of the injection chamber to the furnace makes the entire system difficult to handle certain high-melting-point alloys, as these alloys may cause damage within the system.
In today’s continuously evolving technology landscape, hot chamber die casting remains an important metal forming process. Through continuous optimization and improvement, researchers and manufacturers can overcome its limitations, expand its applicability, and enhance its role in a broader range of industrial applications.
Deconstructing the Components of Hot Chamber Die Casting
One of the core components of hot chamber die casting is the furnace. The furnace is a device that contains metal alloy and heats it to a liquid state. In hot chamber die casting, the furnace typically uses electric or gas heating systems to ensure that the metal maintains a constant high temperature throughout the production process. The design and control of the furnace are crucial for maintaining the stable temperature of the metal, directly affecting the quality and production efficiency of the finished product.
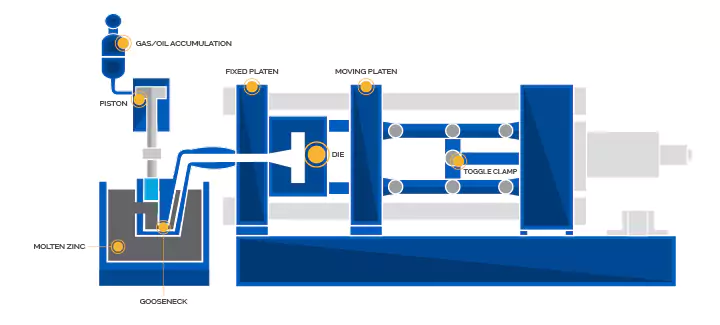
Secondly, the injection chamber is another key component. The injection chamber connects the furnace and the mold, responsible for injecting molten metal into the mold to form the shape of the desired part. The interior of the injection chamber typically includes components such as nozzles, plungers, and fillers, with their design and precision directly determining the accuracy and stability of metal injection. A high-quality injection chamber should have good sealing and high-temperature resistance to cope with the working conditions of high temperature and pressure.
Thirdly, the pressure chamber is another essential component. The pressure chamber is used to apply pressure, pushing the plunger to inject molten metal into the mold. The pressure chamber is usually designed to withstand high-pressure and high-temperature environments to ensure the stability and consistency of the metal injection process. The material selection, structural design, and control of the hydraulic system are crucial factors in ensuring the successful completion of the die casting process.
Additionally, the control system of the hot chamber die casting machine is also a crucial component. The control system is responsible for monitoring and adjusting parameters such as furnace temperature, injection speed, and pressure to ensure the consistency and stability of each production cycle. Advanced control systems can improve production efficiency, reduce energy consumption, and ensure the manufacture of high-quality components.
Navigating the Hot Chamber Die Casting Process
The hot chamber die casting process begins with the preparation of molten metal. In the hot chamber die casting machine, there is a furnace containing blocks of a specific alloy. These materials are heated in the furnace above their melting point, forming molten metal.
Subsequently, molten metal is transported through pipes in the system to the injection chamber. The injection chamber consists of a sealed container, the bottom of which is connected to the furnace. In the injection chamber, the metal remains in a liquid state and awaits the start of the injection process.
When the injection process begins, the nozzle at the bottom of the injection chamber opens, allowing molten metal to enter the connected mold under pressure. The mold is a specially designed metal structure, and its specific shape and size depend on the requirements of the final part. After metal injection, the mold rapidly cools and solidifies, forming the final component.
Compared to cold chamber die casting, one of the main advantages of hot chamber die casting is production efficiency. Due to the liquid state of the metal, reducing cooling time, the entire production cycle is shorter. This is particularly important for mass production and high-volume manufacturing environments.
Assessing the Pros and Cons of Hot Chamber Die Casting
Advantages:
Serial Number | Advantages | Specific Description |
1 | High Production Efficiency | By directly injecting molten metal, cooling time is avoided, making it suitable for large-scale production with shorter production cycles. |
2 | Low Energy Consumption | The metal remains in a liquid state throughout the process, eliminating the need to reheat in each cycle, reducing overall energy consumption and contributing to lower energy costs in the manufacturing process. |
3 | Suitable for Mass Production | Its high efficiency and short cycles make it the preferred choice for large-scale manufacturing, especially in situations requiring high production capacity to meet market demand. |
4 | Economically Efficient | The combination of production efficiency and energy consumption makes it more competitively cost-effective, providing manufacturers with an economically efficient production option. |
5 | High Precision | Due to the metal maintaining a liquid state, the dimensions and shapes of hot chamber die casting products are more accurate, suitable for applications with high precision requirements for components. |
6 | Good Ductility | Suitable for low-melting-point alloys with good ductility, making it applicable to scenarios with high requirements for the shape and structure of components. |
7 | Good Surface Quality of Products | Due to the liquid metal injection, the surface of hot chamber die casting products is usually smooth, eliminating the need for additional surface treatment processes. |
Disadvantages:
Serial Number | Disadvantages | Specific Description |
1 | Limited Application to High-Melting-Point Metals | Mainly suitable for low-melting-point alloys, restricting its application in the manufacturing of high-melting-point metals such as aluminum, magnesium, and other high-melting-point alloys. |
2 | Limited Application to High-Strength, High-Temperature Requirements | Due to material limitations, it may not meet the requirements for components with high strength and high-temperature demands, limiting its application range. |
3 | Difficulty Handling High-Melting-Point Metals Due to Direct Connection of Injection Chamber to Furnace | The direct connection of the injection chamber to the furnace makes it difficult to handle some high-melting-point metals, potentially causing equipment damage or unstable production, increasing technical difficulty. |
4 | Higher Metal Fluidity Requirements Limit Manufacturing of Complex Structures | Some complex structure components may require higher metal fluidity, and the applicability of hot chamber die casting is limited in this aspect. |
5 | Limited to Low-Melting-Point Alloys, Narrow Material Selection | Due to process characteristics, the material selection for hot chamber die casting is relatively narrow, which may become a restricting factor in certain specific applications. |
6 | High Requirement for Mold Wear Resistance, Relatively High Costs | Due to the high-temperature and high-pressure working environment, the molds used in hot chamber die casting require high wear resistance, potentially leading to increased manufacturing costs. |
Exploring Material Choices in Hot Chamber Die Casting
Hot chamber die casting is a pressure casting process mainly used for low-melting-point alloys. Therefore, its primary application materials include zinc alloys, lead alloys, tin alloys, and other low-melting-point metals.
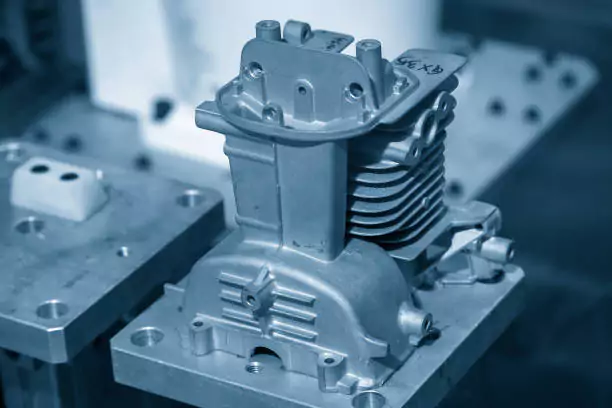
Zinc alloys:
- Composition: Mainly composed of zinc, usually mixed with alloying elements such as aluminum and copper.
- Characteristics: Zinc alloys exhibit excellent fluidity and liquid rheology, making them suitable for complex-shaped components. Their low melting point and good castability make them widely used in hot chamber die casting, especially in the manufacturing of automotive components, electrical enclosures, and more.
Lead alloys:
- Composition: Mainly composed of lead, often alloyed with elements like tin and antimony.
- Characteristics: Lead alloys possess good lubricity and toughness, making them suitable for manufacturing wear-resistant and lubricated components like bearings and pulleys in hot chamber die casting. Their low melting point also facilitates the die casting process at relatively lower temperatures.
Tin alloys:
- Composition: Mainly composed of tin, possibly alloyed with elements like lead and copper.
- Characteristics: Tin alloys have good corrosion resistance and solderability, widely used in manufacturing electronic components’ enclosures, food packaging, and other products requiring corrosion resistance and processability. Their unique properties make tin alloys important in hot chamber die casting.
The role of these materials in hot chamber die casting is primarily reflected in their physical and chemical properties. Firstly, their low melting points allow for the completion of the casting process at relatively lower temperatures, improving production efficiency. Secondly, these alloys typically have good fluidity, facilitating the filling of mold cavities and producing high-precision components. Additionally, specific alloy compositions can impart different properties to the products, such as corrosion resistance and wear resistance, making them suitable for various applications.
Why Steer Clear of Aluminum Alloys?
Applications of hot chamber die casting When selecting materials for hot chamber die casting, aluminum alloys are typically avoided for several reasons:
- High melting point: Aluminum alloys have a relatively high melting point, usually above 600°C, while hot chamber die casting is suitable for low-melting-point alloys like zinc, lead, and tin. Handling high-melting-point metals can be challenging due to the design and working principles of hot chamber die casting machines, potentially leading to equipment malfunctions or unstable production processes.
- Oxidation issues: Aluminum has a high tendency to oxidize and form an oxide layer in high-temperature environments, potentially degrading the surface quality of the products. Hot chamber die casting requires materials to flow smoothly in a liquid state, and the oxide layer on aluminum may impede fluidity, affecting the molding results.
- Equipment adaptability: Hot chamber die casting mechanisms typically need to accommodate lower-melting-point metals, and the high melting point of aluminum may require more complex and expensive equipment design, increasing production costs.
- Cost considerations: Aluminum alloys have higher raw material costs compared to low-melting-point alloys like zinc, lead, and tin. This cost difference may impact the economic feasibility of hot chamber die casting, especially in large-scale production. Lower-cost alloys are more suitable for hot chamber die casting applications, considering factors such as cost, process, and equipment adaptability.
While aluminum alloys are widely used in other casting processes, such as cold chamber die casting and high-pressure casting, the limitations imposed by the characteristics of the process and materials make low-melting-point alloys more suitable for hot chamber die casting. Manufacturers consider factors such as cost, process requirements, and equipment adaptability to choose the most suitable metal materials based on specific needs.
Applications Explored: Hot Chamber Die Casting in Action
Hot chamber die casting, as an efficient metal pressure casting process, has widespread and significant applications in the industrial sector. Its characteristics are mainly reflected in aspects such as production efficiency, economic feasibility, and production precision, making hot chamber die casting a key process in manufacturing.
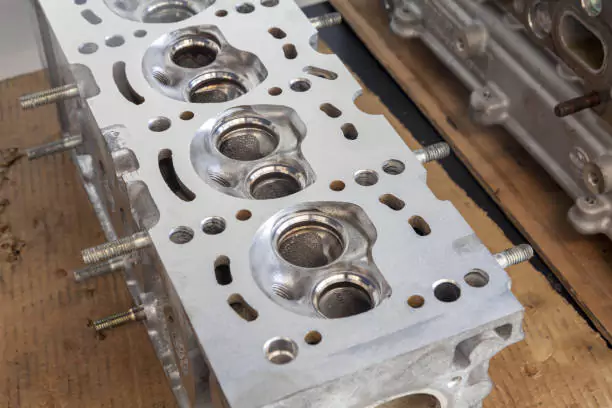
Firstly, hot chamber die casting has significant applications in the automotive manufacturing sector. The production of automotive components requires high production efficiency and precision, and hot chamber die casting is an ideal choice to meet these demands. Engine components, transmission housings, brake system components, and numerous metal components are produced through hot chamber die casting, enhancing production efficiency, reducing manufacturing costs, and ensuring the high precision and reliability of components.
Secondly, hot chamber die casting finds widespread use in the electronics industry. Electronic devices often require metal enclosures to protect internal components and demand that these enclosures have high precision, good thermal conductivity, and electromagnetic shielding performance. The advantages of hot chamber die casting lie in its ability to produce complex-shaped, high-precision metal enclosures, meeting the stringent requirements of electronic products for appearance and performance. Products such as power adapter enclosures and computer housings are commonly manufactured using hot chamber die casting.
Additionally, hot chamber die casting plays a crucial role in the manufacturing of household appliances. In the production of household appliances such as air conditioner housings, washing machine components, and TV brackets, hot chamber die casting provides an ideal solution for manufacturers with its efficient production process and cost-effectiveness. The high precision and flexibility of hot chamber die casting make it a primary choice in the household appliance manufacturing industry.
Finally, hot chamber die casting is widely applied in other fields such as medical equipment manufacturing and communication equipment manufacturing. In these industries, there are strict requirements for component precision, corrosion resistance, and cost control. Hot chamber die casting successfully meets these demands through its efficient production methods and flexible material selection.
In conclusion, hot chamber die casting is a crucial process in various industries, offering efficient and precise manufacturing solutions. Its widespread applications in automotive, electronics, household appliances, and other sectors demonstrate its importance in modern manufacturing.
A Comparative Analysis: Hot Chamber vs. Cold Chamber Die Casting
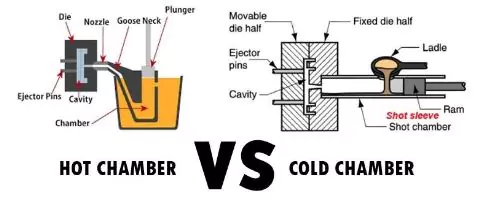
Characteristics | Hot Chamber Die Casting | Cold Chamber Die Casting |
Process Principle | Utilizes direct injection of molten metal, suitable for low-melting-point alloys | Injects molten metal after externally heating it to liquid state, suitable for high-melting-point alloys |
Applicable Materials | Zinc, lead, tin, etc. (low-melting-point alloys) | Aluminum, magnesium, etc. (high-melting-point alloys) |
Production Efficiency | High efficiency, avoids metal cooling time, suitable for mass production | Relatively lower efficiency, needs to consider metal heating and cooling time |
Energy Consumption | Lower, no need to reheat metal in each cycle | Relatively higher, requires reheating metal in each cycle |
Product Characteristics | High precision, good surface quality, suitable for complex structural components | Higher mechanical performance, suitable for components with requirements for strength, heat resistance, etc. |
Equipment Complexity | Relatively simple, straightforward equipment construction | Relatively complex equipment construction, considering metal heating systems, etc. |
Applicable Industries | Mass production, automotive, electronics, etc. | Industries with high requirements for component performance, such as aerospace, defense, etc. |
Common Applications | Electrical housings, automotive components, small industrial parts, etc. | Aerospace components, automotive engine parts, high-strength components in industrial equipment, etc. |
In Summary
Hot chamber die casting is an efficient, low-energy-consumption, and high-precision manufacturing process that holds significant importance in modern manufacturing. BoYi Company maximizes the advantages of hot chamber die casting, offering efficient, reliable, and environmentally friendly solutions for component manufacturing, creating outstanding value for customers.
Key Advantages:
- Efficient Production: Hot chamber die casting, with its direct injection of molten metal, reduces production cycles, making it particularly suitable for mass production.
- Low Energy Consumption: Maintaining the metal in a liquid state throughout the process reduces energy consumption, aligning with the trend of sustainable manufacturing.
- High Precision Manufacturing: The fluidity of liquid metal in hot chamber die casting enables the production of accurately sized and intricately shaped components.
- Material Flexibility: Hot chamber die casting exhibits strong adaptability to various alloys, allowing for diverse material choices based on customer requirements.
BoYi Company has accumulated rich experience in this field, providing high-quality, customized solutions for customers through advanced technology and a professional team, contributing positively to the industry’s development.