At its essence, CNC routing represents a fundamental evolution in manufacturing, characterized by its unmatched precision and adaptability.
CNC Routing Explained
CNC routing is fundamentally a CNC machining technique, employing computer numerical control to guide router tools along material surfaces.
This method intricately sculpts, carves, and molds materials with digital precision, translating virtual designs into physical reality.
Diverging from conventional manual processes, CNC routing streamlines intricate operations, fostering efficiency and precision across diverse manufacturing domains.
A Concise Overview of CNC Routing Evolution
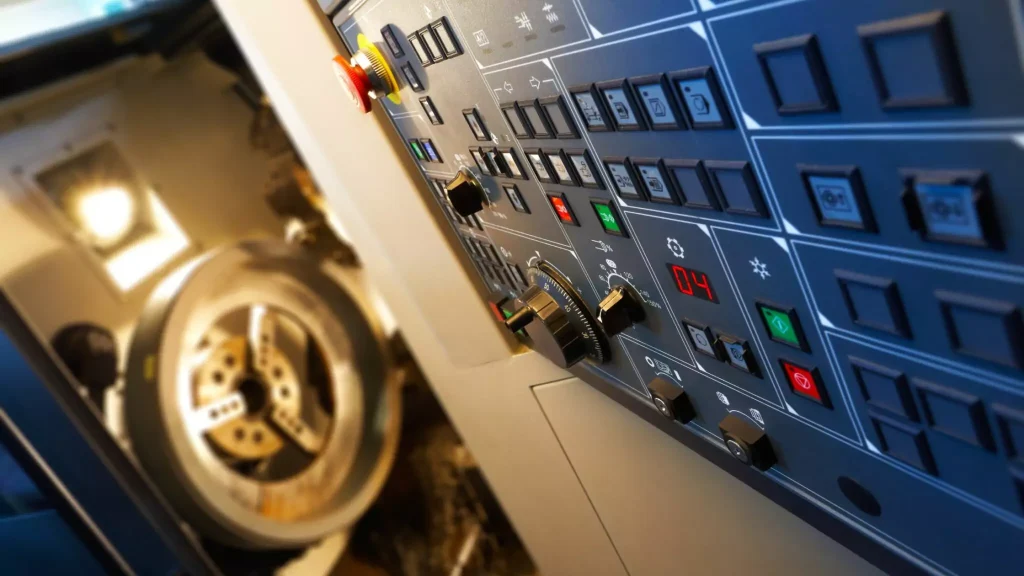
The inception of CNC routing can be traced back to the post-World War II period, characterized by concerted efforts to elevate manufacturing efficiency through technological advancements. Notably, John T. Parsons and Frank L. Stulen, in collaboration with the Massachusetts Institute of Technology (MIT), are acclaimed for spearheading the development of the initial numerical control system in the late 1940s.
This pioneering breakthrough laid the foundation for the subsequent evolution of CNC routing, progressing from rudimentary punched-tape models to sophisticated, computer-driven systems.
Subsequently, Richard J. Kegg made significant strides in furthering the accessibility and advancement of the technology. Kegg’s contributions likely facilitated the widespread integration of CNC routing machines across diverse industrial sectors, revolutionizing manufacturing and fabrication processes.
Understanding the Mechanisms of CNC Routing
At the core of CNC routing operations lies the ability to seamlessly translate digital designs into tangible objects with meticulous precision and efficiency. This process initiates with the creation of a design file on a computer. Employing CAD (Computer-Aided Design) software, intricate designs are meticulously crafted for interpretation by CNC routers.
Following the design phase, CAM (Computer-Aided Manufacturing) software transforms these designs into machine-understandable language, typically G-code. This coding dictates precise movements, cuts, and material shaping to the router, whether the material is wood, metal, plastic, or foam.
The versatility and precision inherent in CNC routing enable the fabrication of a wide array of products, ranging from simple cutouts to intricate three-dimensional structures.
By automating the cutting process, CNC routers mitigate human errors, thereby enhancing both production quality and speed. This technology serves as a cornerstone in industries prioritizing precision, such as furniture manufacturing, sign making, aerospace, and automotive sectors.
Deconstructing the Components of a CNC Router
A profound understanding of a CNC router’s structural composition is imperative for grasping its operational intricacies and the sophistication embedded within its functionalities. Each constituent element assumes a pivotal role, contributing synergistically to the machine’s overall efficacy and adaptability.
Frame
Serving as the backbone of the CNC router, the frame furnishes essential structural integrity to the entire apparatus. Its robustness and stability are paramount, as they determine the machine’s capacity to withstand the formidable forces encountered during routing operations. The frame’s integrity directly correlates with the precision of cuts, as any form of flexure or vibration could precipitate inaccuracies in the machining process.
Motors
The motors embody the powerhouse of a CNC router, orchestrating movement along the X, Y, and Z axes. Typically, two classifications of motors are employed: stepper and servo. Stepper motors navigate in predetermined steps, furnishing meticulous positional control devoid of feedback mechanisms. Conversely, servo motors, complemented by sophisticated feedback systems, adeptly compensate for disparities between anticipated and actual positions, thereby furnishing heightened levels of precision and operational efficiency.
CNC Controller
Functioning as the cerebral nexus of the apparatus, the CNC controller epitomizes computational prowess. This computerized control hub interprets the G-code generated by CAM software, subsequently transmuting it into electrical signals that orchestrate the motors’ movements. It serves as the interactive interface facilitating command input and real-time monitoring of the routing process, thereby ensuring meticulous execution of designs with unparalleled precision.
Gantry
The gantry, akin to a bridge-like structure, spans the cutting table. It accommodates the spindle or router and traverses along the X-axis (from left to right), often supporting movement in the Y-axis (from front to back) for specific designs. Its stability and fluid movement are imperative for achieving precise cuts and intricate details.
Table/Bed
The table, or bed, serves as the platform for securing the material to be cut. Engineered to provide a flat, stable surface, it accommodates various materials securely, utilizing clamps, vacuum hold-downs, or other mechanisms. The table’s design significantly influences the range of materials compatible with the machine and the precision of cuts achievable.
Spindle/Router
Functioning as the primary cutting tool, the spindle or router is accountable for carving, engraving, and shaping the material. Spindles and routers encompass a spectrum of power and speed options, facilitating a broad array of cutting capabilities—from intricate engraving to substantial, aggressive cuts. The selection between a spindle and handheld router is contingent upon project-specific requisites, encompassing material hardness and design intricacy.
Ways
The term “ways” pertains to the linear bearings or guides that facilitate seamless and precise movement of the machine’s mobile components along the axes. Superior-quality ways mitigate friction and wear, ensuring sustained precision and reliability over extended durations.
Axis Drive
The axis drive mechanism, incorporating systems such as rack and pinion or ball screws, converts the rotational motion of the motors into linear displacement. This motion propels the gantry and spindle/router across the material. The choice of drive system profoundly influences the machine’s velocity, accuracy, and capacity to accommodate diverse materials.
Navigating the CNC Routing Process
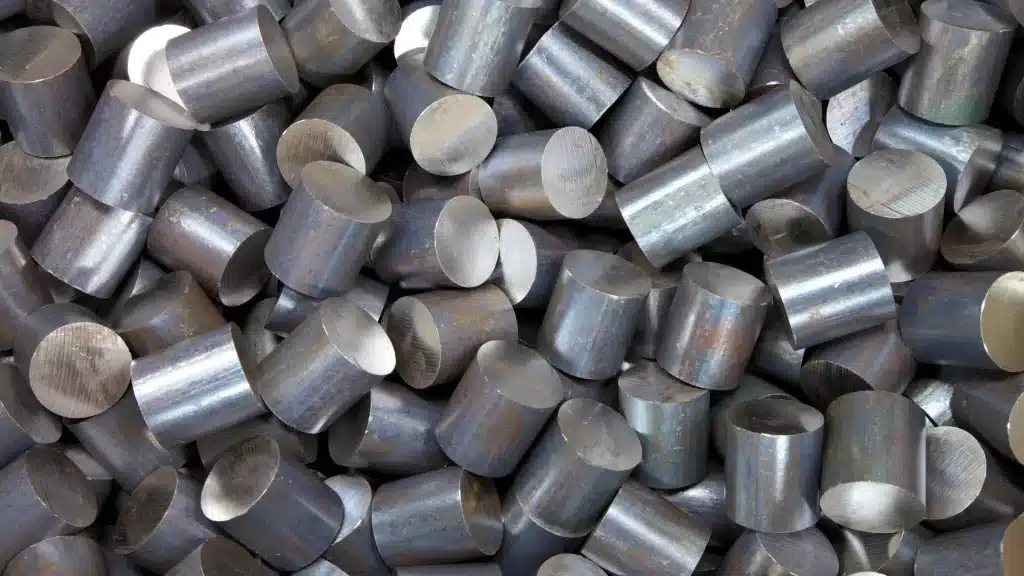
The CNC routing process, intrinsic to industries spanning aerospace to custom furniture, unfolds through a methodical progression of stages. Each stage is indispensable, incrementally constructing the pathway towards a meticulously crafted final product, characterized by exact specifications and superior finishes. Let us traverse through these stages, comprehending their significance within the CNC routing voyage.
Design Creation
Commencing the journey is the stage of design creation, wherein the conceptual blueprint of the final product takes shape. Leveraging CAD software, designers meticulously draft detailed models, laying the groundwork for materialization through the CNC router. This stage assumes paramount importance, as the precision and ingenuity applied directly influence the feasibility and quality of the ultimate piece. Whether destined for intricate artistry or complex machinery, the design phase encapsulates the envisioned outcome in digital form.
Conversion to CNC Language
Subsequent to design creation, the pivotal phase entails the conversion of the CAD model into a language comprehensible to the CNC machine—G-code. Herein, CAM software emerges as the linchpin, translating design intricacies into executable machine directives. Beyond mere translation, this conversion intricately navigates the CNC router’s capacity to faithfully adhere to design paths, considering nuances such as tool paths, cutting depths, and material characteristics. This stage bridges the chasm between digital designs and physical manifestation, accentuating the imperative of precision in CNC operations.
Material Selection and Preparation
Material selection transcends mere aesthetic considerations, delving into the realm of compatibility with functional requisites and CNC router capabilities. Ranging from diverse woods to metals and plastics, materials are chosen based on criteria encompassing durability, finish, and structural integrity. Preparation entails meticulous sizing and secure fixation of the material onto the CNC table, ensuring stability and accuracy during routing. This preparatory stage lays the foundation for metamorphosis, ensuring the selected material is poised for seamless integration with the router.
Machine Setup
Preceding the commencement of operations, meticulous setup of the CNC router assumes paramount significance. This encompasses loading appropriate tools, configuring settings such as speed, feed rate, and tool paths in alignment with material and design specifics. Proper setup is instrumental in optimizing operational efficiency and precision, influencing facets ranging from cut quality to tool longevity. This stage epitomizes the harmonization of machine capabilities with project exigencies, certifying readiness for flawless execution.
CNC Routing Process
With preparatory measures complete, the CNC routing process unfurls as the machine springs into action, executing cuts and carvings in accordance with G-code directives. This stage heralds the materialization of digital designs, with the router meticulously tracing programmed paths to sculpt the physical object. The precision inherent in CNC routing assumes prominence, exemplifying the capability to craft intricate shapes and fine details surpassing manual methodologies.
Post-Processing
Upon completion of routing operations, the post-processing stage undertakes requisite finishing touches to refine the routed piece. This may encompass sanding, painting, or assembly, culminating in the transformation of the routed artifact into its finalized form. Post-processing assumes pivotal significance, addressing both aesthetic appeal and functional efficacy, thereby ensuring alignment with design intent and suitability for intended use.
Quality Control
Concluding the journey is the stage of quality control, dedicated to verifying adherence to specifications and quality standards. This entails meticulous inspection for accuracy, dimensions, and finish, validating the seamless progression of the entire CNC routing process. Quality control stands as the ultimate litmus test, underscoring the precision inherent in the process and affirming the readiness of the product for delivery or utilization.
Exploring Varieties of CNC Routers
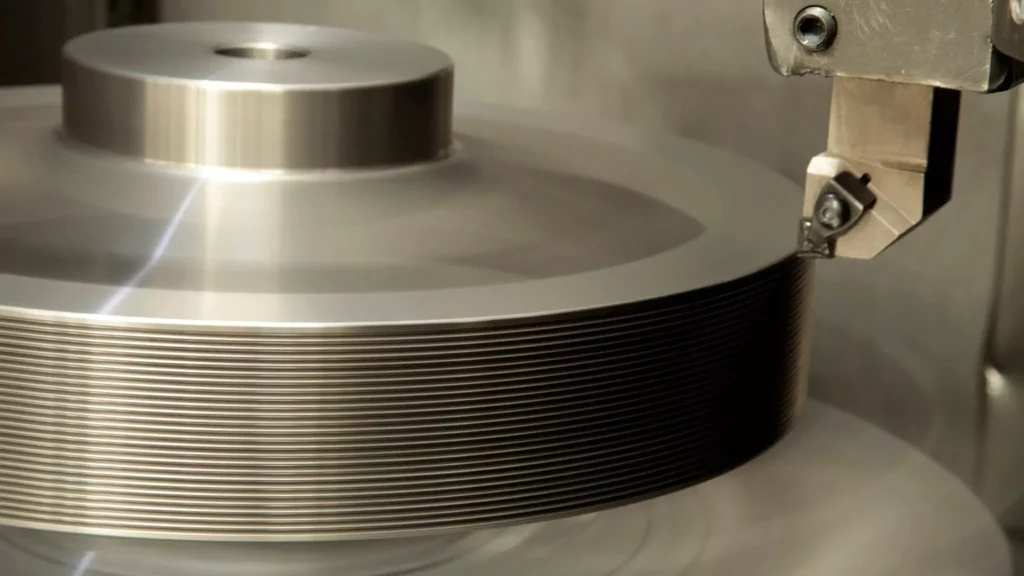
Embarking on a journey into the realm of CNC routing unveils a diverse spectrum of machines, each meticulously crafted to cater to distinct requirements spanning industrial production to individual hobbyist pursuits.
Industrial CNC Routers
At the apex of CNC technology, industrial CNC routers emerge as formidable powerhouses engineered for rigorous utilization within manufacturing ecosystems. Revered for their robust construction and endurance, these routers excel in managing substantial workloads with remarkable swiftness and precision.
They boast sophisticated automation features, encompassing Automatic Tool Changer (ATC) systems and intricate software interfaces tailored to orchestrate multifaceted operations. Principal applications encompass intricate cutting, engraving, and shaping tasks across a broad gamut of materials, prominently deployed in industries such as aerospace, automotive, and furniture manufacturing.
Distinguishing themselves through unparalleled production capacity and precision, industrial CNC routers constitute an indispensable asset for large-scale enterprises.
Desktop CNC Routers
Contrasting the industrial behemoths, desktop CNC routers epitomize compactness, aptly suited for placement within confined workshop spaces or atop desks. Tailored to accommodate smaller-scale projects, prototyping endeavors, and educational initiatives, these routers offer a cost-effective gateway into CNC routing, particularly for novices or those constrained by spatial limitations.
Despite their diminutive stature, desktop CNC routers showcase commendable precision and adaptability, adept at maneuvering through wood, plastics, and soft metals with finesse. Embraced by designers, hobbyists, and burgeoning enterprises alike, their allure lies in their user-friendly interface and minimal maintenance requisites.
Hobby CNC Routers
Versatility characterizes hobby CNC routers, accommodating an array of materials such as wood, plastics, and foams. This adaptability renders them ideal for crafting bespoke items, embellishing home decor, and prototyping innovations.
3-Axis CNC Routers
Constituting the quintessential archetype, 3-axis CNC routers navigate three directions: X (left to right), Y (front to back), and Z (up and down). This inherent versatility facilitates a myriad of cutting, drilling, and milling applications on flat surfaces, making them favored choices across industries and skill levels. The simplicity and efficiency inherent in these machines render them highly accessible, instrumental in fashioning signage, furniture, and intricate designs on a planar canvas.
4-Axis CNC Routers
Elevating the capabilities of their 3-axis counterparts, 4-axis CNC routers introduce an additional axis of rotation, enabling dynamic workpiece maneuverability along the X-axis. This augmentation unlocks the potential for crafting intricate shapes and designs, including sculptures and components necessitating machining on multiple facets. Industries reliant on precision and multidimensional cutting leverage the prowess of 4-axis routers, streamlining operations and augmenting productivity through enhanced geometric intricacies.
5-Axis CNC Routers
At the apex of CNC routing technology lie 5-axis machines, distinguished by their capacity to maneuver along five axes concurrently. This unparalleled flexibility empowers the fabrication of complex shapes, undercuts, and seamless surface finishes. Apt for advanced manufacturing realms mandating intricate design intricacies, such as aerospace and architectural sectors, 5-axis CNC routers epitomize precision and innovation. Their ability to approach the workpiece from varied angles heralds boundless avenues for creativity and ingenuity, propelling industries towards uncharted territories of design excellence.
ATC (Automatic Tool Changer) CNC Routers
Equipped with an automatic tool changing mechanism, ATC CNC routers facilitate seamless tool transitions during the routing process, eliminating the need for manual intervention. This feature significantly bolsters productivity and efficiency, particularly in scenarios necessitating the use of multiple tool types.
ATC routers thrive in production environments characterized by stringent time constraints and exacting precision requirements. Their unparalleled ability to curtail downtime and mitigate human error renders them indispensable assets for high-volume, intricate projects.
Nested-Based CNC Routers
Tailored to optimize material utilization and operational efficiency, nested-based CNC routers strategically arrange cutting patterns to minimize waste. This variant finds favor in industries engaged in furniture manufacturing, cabinetry, and sheet metal fabrication, where maximizing material yield assumes paramount importance.
Combining software-driven optimization with precision cutting capabilities, nested-based CNC routers offer a synergy of economic and environmental advantages. By reducing waste while upholding stringent production standards, these routers exemplify a harmonious balance between efficiency and sustainability.
Exploring CNC Routing Operations
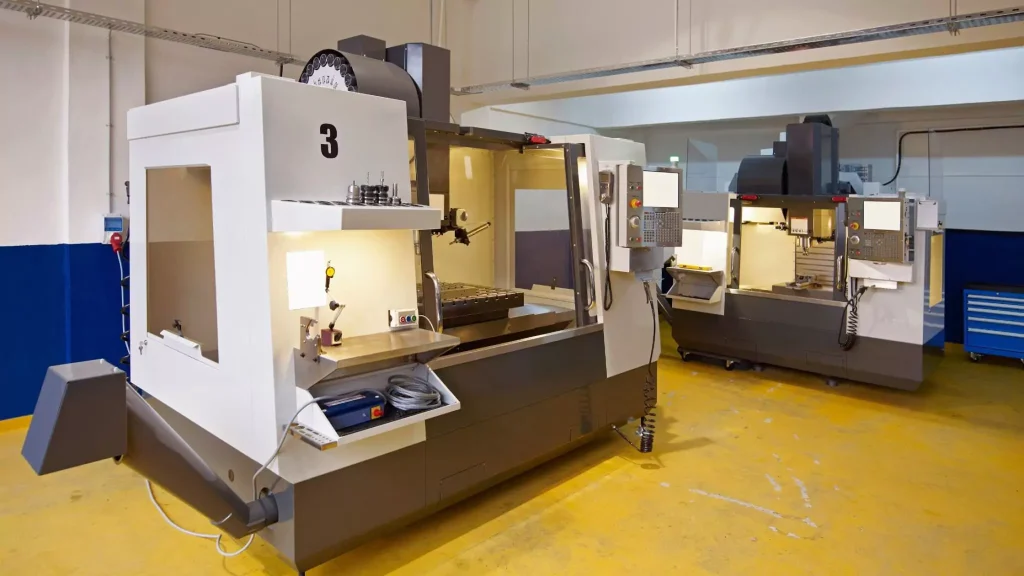
CNC routing operations encompass a diverse array of meticulously orchestrated processes, each tailored to manipulate materials in alignment with precise design and manufacturing requisites.
Engraving
Exemplifying precision craftsmanship, engraving entails the meticulous carving of intricate patterns, letters, or images onto material surfaces. Typically, this operation necessitates CNC routers equipped with fine cutting tools or spindles to achieve requisite detail and depth. Engraving finds application in:
- Crafting detailed artwork on various substrates such as wood, metal, or acrylic.
- Fabricating signage adorned with intricate logos or typography.
- Personalizing items through the addition of names, dates, or messages.
- Manufacturing industrial labels and control panels featuring precise, enduring markings.
Profiling
Central to the fabrication process, profiling involves the precise extraction of shapes from material substrates along defined outlines, yielding components or features with exacting dimensions. Machines endowed with robust drive systems and versatile cutting tools are instrumental in executing profiling operations. This operation is indispensable for:
- Manufacturing components boasting specific contours or shapes tailored to exact specifications.
- Refining part edges to attain seamless, polished boundaries.
- Crafting decorative panels or architectural elements boasting intricate outlines and configurations.
Pocketing
Akin to sculpting material substrates, pocketing entails the meticulous removal of material from a workpiece’s surface to engender cavities or recesses of predetermined depths. CNC routers boasting precise cutting depth adjustments are indispensable for executing pocketing tasks, serving diverse purposes such as:
- Generating recesses accommodating inlays or fitting components seamlessly.
- Machining slots or channels integral to the structural integrity and functionality of the workpiece.
- Fabricating cavities within molds or dies pivotal to manufacturing applications spanning various industries.
Drilling
Integral to CNC routing, drilling entails the creation of cylindrical holes within material substrates, spanning from straightforward, linear bores to intricate, angular ingress and egress points. Machines boasting precise z-axis control excel in this operation, utilized for:
- Preparing components for assembly via screws, bolts, or dowels.
- Establishing ventilation apertures or conduits within intricate components.
- Forming apertures for electrical or plumbing wiring and piping applications.
3D Carving
Pushing the boundaries of CNC routing into the third dimension, 3D carving involves the sculpting of materials to fashion shapes imbued with depth, contours, and intricate detailing. This operation mandates routers endowed with comprehensive control over all three axes, applied in:
- Crafting statues, sculptures, or embellishments adorned with elaborate geometries.
- Fabricating molds integral to casting or thermoforming processes.
- Generating prototypes or models for evaluative or demonstrative purposes.
The capacity to carve in three dimensions unveils boundless avenues for innovation and expression, facilitating the production of objects characterized by intricate detailing and complex geometries.
Reaming
Epitomizing precision refinement, reaming serves as a finishing operation aimed at fine-tuning hole sizes and enhancing surface finishes. Machines distinguished by high precision and stability excel in this operation, ensuring:
- Holes exhibit precise diameters, catering to tight-tolerance fittings.
- Internal hole surfaces boast smooth textures devoid of burrs or imperfections.
- Components coalesce seamlessly with exact alignment during assembly.
Reaming elevates the caliber and functionality of parts, particularly in applications where precision fitting and alignment are paramount considerations.
Threading
Central to component assembly, threading involves the creation of helical structures along material surfaces, catering to fastening applications such as screws and bolts. CNC routers, outfitted with specialized tool heads, execute threading operations by harmonizing spindle rotation with linear material or tool motion. Precision control, facilitated by advanced CNC systems, ensures the seamless execution of programmed tool paths, manifesting in:
- Precision Fastening: Ensuring components conjoin with exacting tolerance levels.
- Custom Thread Patterns: Tailoring thread designs to bespoke specifications for specialized applications.
- Automated Production: Streamlining manufacturing workflows to enhance efficiency and consistency.
- Material Versatility: Adapting seamlessly to diverse materials, spanning metals to plastics, while upholding accuracy benchmarks.
Ramping
Elevating machining precision, ramping epitomizes the technique of gradually entering or exiting material surfaces at an angle rather than via perpendicular plunges. This strategic approach minimizes tool load, mitigating wear and the risk of breakage. Guided by CAM software programs, CNC routers execute ramping with controlled movements, yielding:
- Enhanced Tool Life: Prolonging cutting tool durability by curbing impact forces.
- Improved Surface Finish: Attaining smoother surfaces devoid of unsightly tool marks.
- Versatile Cutting Strategies: Adapting seamlessly to intricate geometries and challenging-to-access regions.
- Efficient Material Removal: Optimizing cutting processes to expedite production timelines without compromising on quality benchmarks.
Slotting
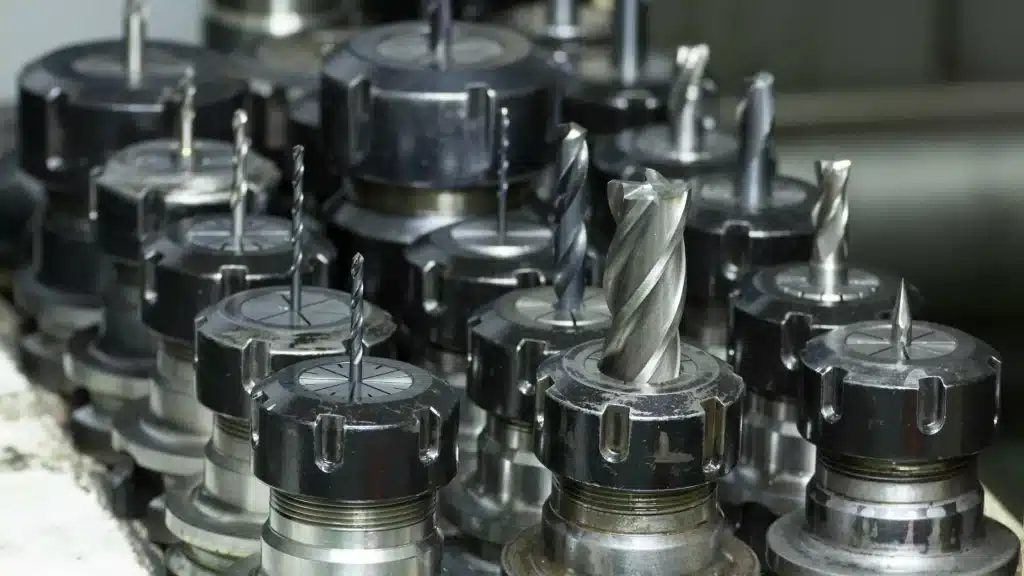
Integral to diverse manufacturing endeavors, slotting entails the precision cutting of narrow grooves or slots within materials. CNC routers, harnessing precision control over the X, Y, and Z axes, excel in slotting operations. Leveraging high-speed spindle motors and apt cutting tools, CNC routers deliver:
- Component Assembly: Facilitating interlocking parts in furniture and structural frameworks through strategically crafted slots.
- Ventilation Features: Integrating airflow channels within electronic enclosures and automotive components.
- Decorative Detailing: Enhancing product aesthetics through intricately fashioned slot patterns.
- Functional Grooves: Catering to wiring, piping, and other utilitarian requisites in multifaceted projects.
Facing
At the outset of the manufacturing process, facing involves the creation of a pristine, flat surface on a workpiece. CNC routers meticulously execute facing operations by traversing a cutter across the material surface, ensuring uniformity and a flawless finish. This operation is pivotal for:
- Surface Preparation: Establishing material flatness as a foundation for subsequent machining processes.
- Thickness Calibration: Attaining exact material thickness to uphold quality standards and uniformity.
- Aesthetic Enhancement: Elevating the visual allure of material surfaces to meet stringent aesthetic criteria.
- Base Formation: Establishing a stable foundation for intricate machining endeavors, augmenting overall precision.
Chamfering
Chamfering entails the precise removal of material to create beveled edges, serving both aesthetic and functional ends such as facilitating assembly. CNC routers, renowned for their precision and adaptability, excel in chamfering operations, accommodating diverse angles and depths tailored to project specifications. This process is instrumental in:
- Edge Refinement: Smoothing sharp edges to enhance safety, handling, and visual aesthetics.
- Assembly Facilitation: Preparing components for seamless and secure assembly.
- Stress Mitigation: Alleviating stress concentrations in materials prone to fracture or failure.
- Ornamental Embellishment: Infusing products with distinctive design elements for heightened aesthetic appeal.
Parting/Cutting Off
Parting or cutting off involves the precise separation of a part from the parent material, a common practice in fabricating individual components from larger stock. CNC routers execute this operation with exacting precision, delivering clean and accurate cuts facilitated by intricate tool path management and consistent cutting force application. This technique encompasses:
- Component Segmentation: Efficient production of individual parts from bulk material stock.
- Material Optimization: Minimizing waste through maximal utilization of material resources.
- Precision Machining: Attaining precise component dimensions critical for assembly and functionality.
- Material Versatility: Adapting cutting methodologies to a diverse array of materials ranging from wood to advanced composites.
Inlaying
Inlaying epitomizes the embedding of one material within another to fashion decorative patterns or reinforce structural integrity. Leveraging precise depth and positioning control, CNC routers excel in intricate inlay work, exemplifying their capacity to undertake delicate tasks and yield exquisite outcomes that merge functionality with aesthetic finesse. This technique encompasses:
- Ornamental Detailing: Crafting elaborate patterns and artwork enhancing the allure of furniture, musical instruments, and decorative artifacts.
- Structural Fortification: Reinforcing objects through strategic material integration in key areas.
- Custom Branding: Incorporating logos or brand insignia directly into products for distinctive identity.
- Material Fusion: Harmonizing disparate materials to achieve unique aesthetic effects or fulfill specialized performance requirements.
Analyzing CNC Router Power Consumption
The electricity consumption of a CNC router can fluctuate significantly, typically ranging from 3 to 20 kW per hour, contingent upon factors such as machine size and complexity. Industrial-grade models, particularly when operating at full capacity, may incur higher power demands, thus influencing operational expenditures.
Adopting efficient usage practices and comprehending the machine’s power requisites are essential strategies for effectively managing electricity costs.
Understanding CNC Router Noise Levels
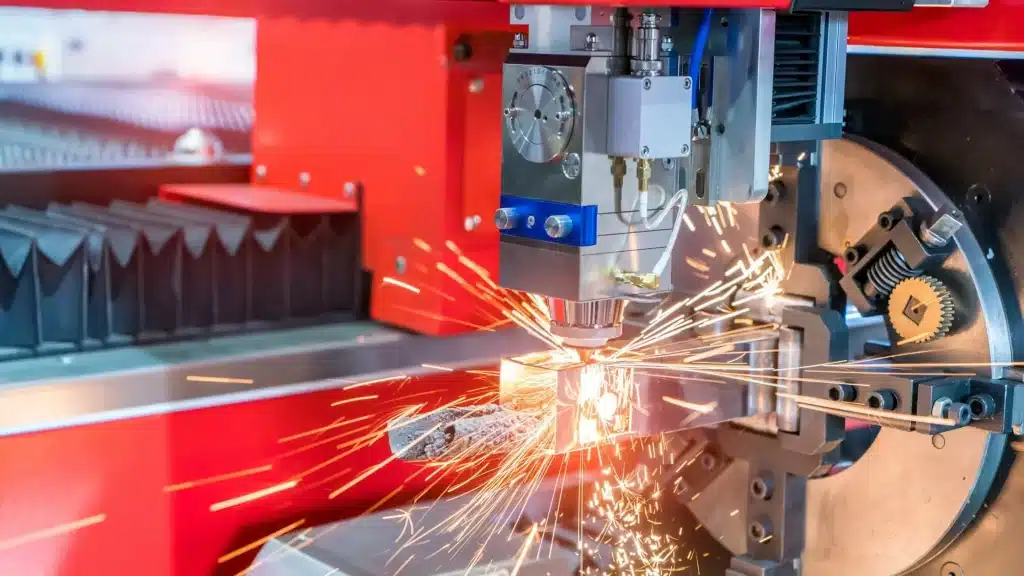
In addition to their renowned precision, CNC routers are characterized by notable noise emissions, typically registering between 70 to 100 decibels.
The intensity of sound is contingent upon various factors, including the specific machining operation, material composition, and cutter type. In industrial environments, the implementation of hearing protection measures is often imperative to mitigate the risk of auditory impairment during prolonged machine utilization.
Distinguishing CNC Milling from Routing
While CNC milling and routing share similarities in their computer-controlled machining methodologies, they diverge notably in their applications and material processing techniques.
CNC milling is tailored for robust, precision cuts in dense materials like metals, employing elevated torque levels and reduced rotational speeds. Conversely, routing excels in the fabrication of softer materials such as wood, plastics, and foam, characterized by swift operation speeds albeit with diminished torque.
Exploring the Contrast Between a CNC Router and Spindle
The disparity between a CNC router and a spindle resides primarily in their functional roles within the CNC domain.
A CNC router constitutes the entirety of the machine apparatus engineered for cutting, carving, and engraving across diverse material substrates.
In contrast, the spindle serves as a pivotal component within the router assembly, functioning as the motor-driven apparatus responsible for securing and rotating cutting tools. Its significance lies in dictating the speed and precision of machining operations, thus exerting a profound influence on the router’s overall performance and efficacy.
Strategic Considerations in CNC Routing
In conclusion, CNC routing emerges as an adaptable and exacting methodology for material machining, its economic implications shaped by factors such as machine classification, material characteristics, design intricacy, and operational duration.
While pragmatic concerns such as electricity consumption and noise emissions warrant attention, a nuanced grasp of the divergent functionalities encompassed by CNC milling, routing, and pivotal components like spindles enriches the understanding of this technology’s expansive utility.
By assimilating these discernments, stakeholders can make well-informed choices and optimize the utilization of CNC routing across diverse operational contexts.